反應(yīng)堆溫差法液位傳感器的研究
發(fā)布時間:2020-10-29
瀏覽次數(shù):
摘要:國內(nèi)新建的三代核電技術(shù)基于安全考慮,提出了溫差法液位測量技術(shù)。本文據(jù)此設(shè)計了一種基于溫差法的
液位傳感器。其根據(jù)水與水蒸氣的傳熱系數(shù)的顯著差異,通過安裝于電加熱器加熱區(qū)處
熱電偶與遠(yuǎn)離加熱區(qū)熱電偶之間的測量溫度差值,判斷測點處液位情況。通過軟件模擬計算和試驗實測數(shù)據(jù),證實了所設(shè)計的液位傳感器結(jié)構(gòu)設(shè)計合理,性能可靠,能夠有效地判斷反應(yīng)堆內(nèi)液位變化情況。
反應(yīng)堆壓力容器內(nèi)液位是涉及反應(yīng)堆安全保護(hù)和反應(yīng)堆事故后監(jiān)測的重要參數(shù)。目前,國內(nèi)新建的第三代核電技術(shù)基于更高的安全要求,放棄了需要在壓力容器上開孔的壓差式液位測量方法。傳統(tǒng)的工業(yè)液位計種類很多,如浮力式水位計、超聲波水位計、電接點式水位計、電容和電感式水位計等,然而能夠在具有高溫、高壓以及高輻照環(huán)境的反應(yīng)堆壓力容器內(nèi)部,實現(xiàn)液位測量的傳感器較少。溫差法液位傳感器作為一種成熟技術(shù),能夠?qū)崿F(xiàn)反應(yīng)堆液位的定點測量,其結(jié)構(gòu)簡單,主要由電加熱器和熱電偶組成,受環(huán)境影響較小,具有很高的可靠性,目前廣泛被第三代核電技術(shù)所采用。
1液位傳感器原理與設(shè)計
1.1傳感器測量原理
液位傳感器通過ΔT的方法進(jìn)行液位測量,主要由1個電加熱器和2個熱電偶組成。其中,一個熱電偶處于電加熱器的加熱區(qū)內(nèi),用于進(jìn)行水位判讀(水位測點);一個熱電偶處于距離加熱區(qū)一定距離的非加熱區(qū)內(nèi),用于測量環(huán)境溫度。
由水和水蒸氣或空氣的物性參數(shù)可知,水的換熱系數(shù)與水蒸氣的換熱系數(shù)存在著較為明顯的差別,當(dāng)水位測點(電加熱器加熱區(qū)的熱電偶)位于水中時,由于水具有更高的換熱系數(shù),熱電偶測得的溫度值相對較低,而當(dāng)水位測點處于水蒸氣中時,水蒸氣換熱系數(shù)較低,熱電偶測得的溫度值相對較高。
在進(jìn)行水位測量時,將加熱熱電偶和非加熱熱電偶共同組成一個水位測點,采用溫差輸出值ΔT來判定水位,即
ΔT=(Tch-Tcr)(1)
式中:Tch為位于加熱區(qū)域的熱電偶溫度;Tcr為遠(yuǎn)離加熱區(qū)域的熱電偶溫度。通過水位測點在水中和水蒸氣中的溫度差別,可設(shè)定一個合理的溫差值20℃,當(dāng)ΔT的數(shù)值大于該溫差值時,表明水位測點處于水蒸氣中;如果ΔT的數(shù)值小于該溫差值時,則水位測點處于水中。如果沿水位高度布置若干個液位傳感器,便可判斷出壓力容器內(nèi)部液位所處的高度范圍。液位傳感器測量原理如圖1所示。
1.2傳感器結(jié)構(gòu)設(shè)計
根據(jù)液位傳感器的測量原理,其結(jié)構(gòu)主要包括1個電加熱器、1個作為測點的位于加熱器加熱區(qū)的熱電偶和1個作為參考點的位于非加熱區(qū)的熱電偶。由于傳感器位于反應(yīng)堆壓力容器內(nèi)部,傳感器外部有對傳感器進(jìn)行固定的不銹鋼外殼,不銹鋼外殼將一回路的水隔離開,外殼內(nèi)部為導(dǎo)熱系數(shù)特別低的空氣。為增加加熱區(qū)部位測點的熱量傳導(dǎo)效率,提升傳感器的響應(yīng)時間,在熱電偶的熱端設(shè)計了導(dǎo)熱塊結(jié)構(gòu),液位傳感器的結(jié)構(gòu)設(shè)計如圖1所示。

1.3傳感器理論分析
液位傳感器的測點可以近似地看作一個圓柱體的傳熱結(jié)構(gòu)。由于液位傳感器的結(jié)構(gòu)相對復(fù)雜,包含了各種不同的材料,同時導(dǎo)熱塊需要通過熱電偶,其結(jié)構(gòu)為異形結(jié)構(gòu),從而導(dǎo)致液位傳感器無法簡單地利用傳熱公式進(jìn)行計算。為保證液位傳感器計算的正確率,在此使用ANSYS有限元分析軟件對液位傳感器進(jìn)行建模分析,傳感器內(nèi)部的材料傳熱系數(shù)可以通過查詢相關(guān)資料進(jìn)行確定,此時僅需要對外殼與環(huán)境之間的換熱系數(shù)進(jìn)行確定。
液位傳感器在正常工作時,測點不銹鋼外殼外部的水或水蒸氣無強制對流,因此測點外部的水或水蒸氣可視為自然對流,測點外殼的換熱系數(shù)為相應(yīng)的自然對流換熱系數(shù)。相應(yīng)地自然對流換熱系數(shù)[1]為

式中:h為對流換熱系數(shù),W/(m2·℃);Pr為普朗特數(shù),表示流體傳遞動量與傳遞熱量的能力之比;Gr為格拉曉夫數(shù),表示自然對流中的驅(qū)動力,浮升力與黏性力之比;C,n為常數(shù),依據(jù)Gr和Pr取值;λ為流體的熱導(dǎo)率,W/(m·K);l為特征長度,液位傳感器加熱區(qū)長度;g為重力加速度,m/s2;α為流體的力膨脹系數(shù);ν為運動黏度;m2/s;ΔT為流體與壁面的溫差,K。
由于探測器實際工作時位于內(nèi)徑為13mm的導(dǎo)向管中,而非在無限大空間中。因此,通過式(2)計算出的自然對流系數(shù)需要考慮有限空間的影響,對傳熱系數(shù)進(jìn)行相應(yīng)修正。
2軟件仿真計算
反應(yīng)堆正常工作時液位傳感器外部的水處于高溫高壓狀態(tài),其設(shè)計工作溫度為343℃。當(dāng)反應(yīng)堆出現(xiàn)泄漏事故時,壓力容器內(nèi)部由于壓力減小,水持續(xù)蒸發(fā)導(dǎo)致水位不斷下降,在傳感器測點露出水面后,傳感器的溫差值將迅速上升超過報警閾值,從而引發(fā)報警信號。
為驗證液位傳感器設(shè)計的合理性,使用ANSYS有限元分析軟件將液位傳感器進(jìn)行建模仿真計算,分別計算液位傳感器位于水中和位于水蒸氣中時的測點溫度分布。
反應(yīng)堆正在工作時其壓力容器內(nèi)部溫度為343℃,根據(jù)式(2)計算該溫度下測點位于水中和水蒸氣中的換熱系數(shù),同時考慮傳感器工作于內(nèi)徑13mm的導(dǎo)管內(nèi)部,相應(yīng)的導(dǎo)熱系數(shù)需要進(jìn)行修正,其中水蒸氣由于有限空間的影響,其導(dǎo)熱系數(shù)需要相應(yīng)地降低。在計算水的導(dǎo)熱系數(shù)時,考慮到反應(yīng)堆在出現(xiàn)泄漏后,由于壓力降低,并且測點的電加熱器處于持續(xù)加熱狀態(tài),測點部位的水將處于沸騰狀態(tài),而水沸騰將極大的提高導(dǎo)熱系數(shù)。因此,在進(jìn)行仿真計算時,綜合式(2)自然對流換熱系數(shù)計算數(shù)據(jù),以及液位傳感器的實際工作狀態(tài),設(shè)定傳感器分別位于水蒸氣與水中時的換熱系數(shù)。
將相應(yīng)的數(shù)據(jù)輸入軟件后,根據(jù)模擬結(jié)果與性能要求對比,將加熱功率穩(wěn)定為20W時液位傳感器性能最佳,所得計算結(jié)果如圖2所示。
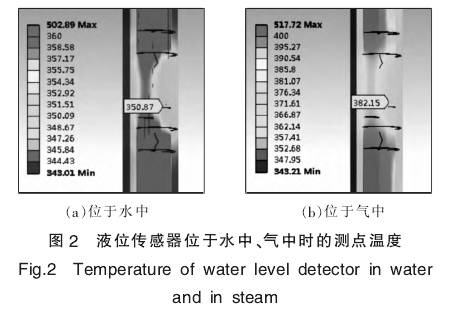
為驗證液位傳感器的響應(yīng)特性,對測點進(jìn)行瞬態(tài)分析。由于軟件較難模擬水位下降的過程,模擬時假定測點外部的環(huán)境瞬時由水變?yōu)樗魵猓瑴y點相應(yīng)的溫差值變化曲線如圖3所示。
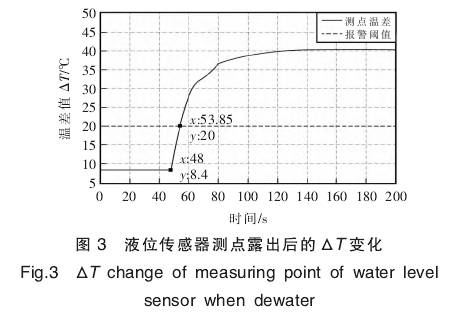
根據(jù)仿真計算結(jié)果,液位測點在位于水中時溫差約為8.4℃,遠(yuǎn)低于報警閾值20℃,能夠確保液位傳感器不會出現(xiàn)誤報警;在測點露出水面之后,測點的溫差值僅經(jīng)過約5.85s就達(dá)到報警閾值20℃,具有非常高的響應(yīng)速度,所設(shè)計的液位傳感器滿足相應(yīng)設(shè)計要求,能夠有效反饋液位變化。
3熱工試驗及分析
根據(jù)液位傳感器的軟件仿真計算結(jié)果,制作了液位傳感器樣件,并對樣件進(jìn)行熱工臺架試驗。熱工試驗如圖4所示。由圖可見,液位傳感器樣件安裝在模擬反應(yīng)堆實際工況的熱工臺架中,熱工臺架通過電加熱器對壓力容器內(nèi)的水進(jìn)行加熱升溫,在壓力容器內(nèi)部的溫度上升到指定溫度后,打開底部閥門排出壓力容器內(nèi)的水,使壓力容器內(nèi)部水位下降,模擬反應(yīng)堆失水事故,此時對液位傳感器的性能進(jìn)行測試。
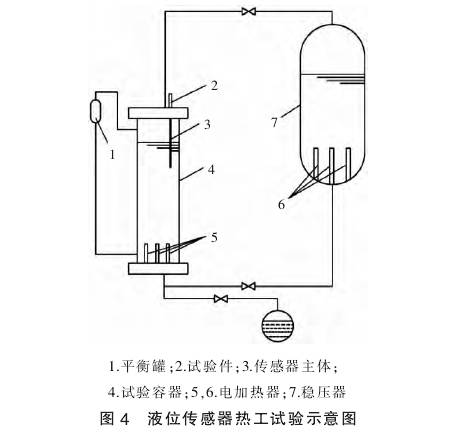
液位傳感器在反應(yīng)堆正常工作溫度343℃的溫度平臺上進(jìn)行液位下降試驗。試驗測試了2種功率水平下傳感器的工作狀況,分別為與仿真模擬一致的20W加熱功率以及更高的功率25W。2種功率水平下傳感器的溫差曲線如圖5所示。
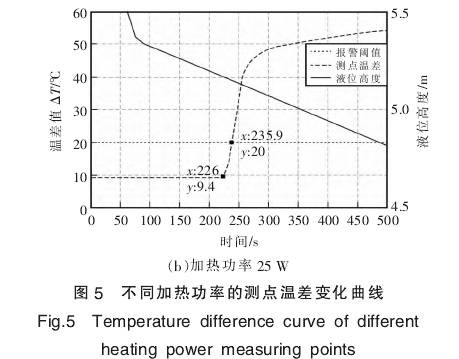
試驗過程中待液位傳感器在水中溫度穩(wěn)定后,開啟壓力容器底部閥門,壓力容器內(nèi)部的液位高度開始降低,當(dāng)液位下降到測點露出水面以后,測點的溫差值就開始快速上升,最終超過設(shè)定的溫差閾值。相應(yīng)的試驗數(shù)據(jù)與模擬計算結(jié)果對比見表1。

由試驗數(shù)據(jù)可知,液位傳感器在液位降低到測點所在位置后能正確響應(yīng)。
在進(jìn)行傳感器25W加熱功率試驗時,由于電加熱功率的提升,測點水中溫差、水蒸氣中溫差以及升溫速率高于20W加熱功率試驗時的數(shù)據(jù),而傳感器20W加熱功率時的試驗數(shù)據(jù)相較于模擬計算得出的數(shù)據(jù),其水中溫差更低,水蒸氣中的溫差值更高,而升溫速率遠(yuǎn)低于模擬計算結(jié)果。結(jié)合試驗的實際情況,分析出產(chǎn)生相應(yīng)偏差的原因如下:
①傳感器材料的傳熱系數(shù)實際上是隨溫度變化的,計算時認(rèn)為其為固定值;
②傳感器外殼的導(dǎo)熱系數(shù)為理論計算之后的修正值,實際傳感器正常工作時環(huán)境較為復(fù)雜,其導(dǎo)熱系數(shù)與理論計算具有一定偏差;
③模擬計算時傳感器整體瞬間從水中變?yōu)樗魵庵校鴮嶋H試驗時液位是緩慢下降的,測點表面也會殘留水膜,因此傳感器的實際升溫速率會低于理論計算結(jié)果。
4結(jié)語
液位傳感器的仿真計算與實際試驗數(shù)據(jù)的對比表明,該液位傳感器的測量原理簡單可靠,結(jié)構(gòu)設(shè)計合理,具有較高的可靠性,能夠有效地反應(yīng)液位變化;仿真計算較為符合工程實際,較為真實地反應(yīng)傳感器特性。液位傳感器位于水中與位于水蒸氣中的溫差值差別大,具備較高的分辨率,能夠有效判斷液位的變化情況,適用于反應(yīng)堆這種對于液位測量要求較高的場合;測點在露出水面后能夠快速升溫,具有較高的響應(yīng)速度,能夠及時反饋液位變化情況;能夠通過調(diào)節(jié)加熱功率控制測點溫差的幅度,以此匹配不同水溫情況下的不同導(dǎo)熱系數(shù),保證液位探測器能夠在較廣的溫度范圍內(nèi)正常工作。